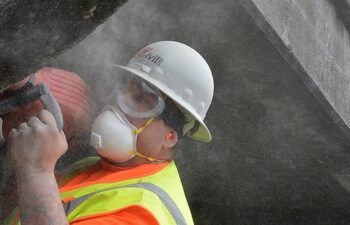
When it comes to maintaining a commercial property, one of the most critical aspects is to ensure the integrity and safety of the concrete structures. Over time, concrete can sustain damage from various factors, such as weather conditions, heavy traffic, and settling. Repairing commercial concrete damage is an essential process that requires professional help and specialized techniques.
We at U.S. Pave understand the importance of being well-informed about the commercial concrete repair process. By gaining insight into the professional approach, property owners and managers can ensure they make the right choice when selecting a concrete repair company and effectively communicate their concerns and requirements. Understanding the tasks involved also helps manage expectations and anticipate the different stages of repair. Here’s an easy-to-understand guide on how professionals repair commercial concrete effectively:
Determine the Cause of Damage
Visually inspecting, testing, and analyzing the concrete structure can help determine the root cause of the problem and identify any underlying issues that may have contributed to the damage. Common causes of damage to commercial concrete structures include:
- Freeze-thaw cycles: When water enters the pores of concrete and then freezes, it expands and creates pressure on the surrounding concrete, leading to cracks and other forms of damage.
- Chemical exposure: Exposure to chemicals such as acids, salts, and alkalis can damage concrete, causing the surface to deteriorate or discolor.
- Heavy traffic: Constant vehicular or foot traffic can cause wear and tear on concrete surfaces over time.
- Moisture intrusion: Water infiltration can cause damage to concrete surfaces, especially if left untreated for a long time.
- Structural issues: Problems with the underlying structure of a concrete surface, which the settling or shifting of the ground beneath the concrete or poor construction practices can cause, can result in cracking or other forms of damage.
Assess the Severity of the Damage
We employ various methods, such as visual inspection, non-destructive testing, and core sampling, to assess the extent of the damage and determine the scope of repair work required. It’s common for us to perform a concrete soundness test at this stage. This test helps evaluate the structural integrity and overall condition of the concrete surface. By tapping the surface with a specialized hammer, we can identify areas with hollow or delaminated sections that may require further attention.
Evaluate Whether Repairs Are Necessary
Factors such as cost, time, and safety considerations should determine the decision to repair or replace damaged concrete. In some cases, it may be more cost-effective to replace damaged concrete rather than attempt to repair it. This decision typically depends on the extent of the damage and the feasibility of implementing repairs without compromising the structural integrity of the entire surface.
In addition, the expected life span of the repaired concrete should be evaluated in terms of future maintenance costs and potential safety hazards. A skilled and experienced concrete repair company such as U.S. Pave will carefully weigh these factors to provide an informed recommendation on the best course of action for the specific situation.
Identify the Best Solution
The best solution for repairing commercial concrete damage should consider factors such as the type and extent of damage, the location of the damage, and the desired outcome. This helps select the best-suited repair method or product to address the problem. Some of the most common repair methods include:
Dry-Pack
A mixture of sand and cement is used to create a stiff, dry mixture that is packed into the damaged area. The mixture is then tamped down and smoothed out to create a level surface. Dry-pack is often used for repairing small areas of damage, such as cracks or chips.
Preplaced Aggregate Concrete
Coarse aggregate is placed into the damaged area before the concrete mix is poured in. The concrete mix then surrounds the aggregate, creating a strong bond between the two materials. Preplaced aggregate concrete is often used to repair larger areas of damage, such as potholes or large cracks.
Synthetic Patches
These patches are made from synthetic materials, such as epoxy or polyurethane, and are designed to adhere to the existing concrete surface. The patch is then filled with a concrete mix and smoothed out to blend in with the surrounding area. This method is relatively new, but it’s becoming increasingly popular as an alternative to traditional concrete.
Concrete Replacement
This method involves completely removing the damaged concrete section and pouring in a new section to replace it. It’s generally applied when the extent of the damage is severe, and it’s more feasible to reconstruct the affected area. Concrete replacement ensures a fully restored and long-lasting solution that can withstand future wear and tear.
Prepare the Area for Repair
Proper preparation of the area for repair is essential for ensuring a successful repair job. This involves removing any loose debris or contaminants from the damaged area. It also means preparing any surrounding areas that may be affected by the repair process by removing dirt, vegetation, and other objects.
Repair the Damaged Concrete
The repair method used will depend on factors such as the type and extent of the damage, as well as any specific requirements or constraints related to the project. In many cases, this may involve reinforcing the repair area with additional support from rebar or wire mesh to provide added strength and stability. Following proper repair techniques and using high-quality materials is important to ensure a long-lasting repair.
Cure and Protect the Repaired Area
Proper curing and protection of repaired concrete are essential for ensuring its longevity and durability. This involves allowing sufficient time for curing before subjecting it to heavy traffic or other stresses. It may also mean applying a protective coating or sealant to prevent future damage.
Repairing commercial concrete damage requires specialized equipment and a high level of expertise. If you have any questions about the repair process or you’re considering having repairs done at your commercial property, feel free to contact us at U.S. Pave. Our team of experienced professionals is dedicated to providing innovative solutions and exceptional service.
GP Caveman Bridge Concrete repair by Oregon Department of Transportation is licensed with CC BY 2.0
Posted on behalf of
U.S. Pave is a full-service paving maintenance and installation company serving all of Florida with Parking Lot Maintenance, New Asphalt Construction, Asphalt Patching and Repair, Parking Lot Crack Repair, Pothole Repair, Parking Lot Resurfacing (Overlay), Parking Lot Sealcoating or Resealing, Concrete Maintenance, Concrete Flatwork, Concrete Car Stops, Flow line / Curb & Gutter, Trip-hazard Removal/Grinding, Parking Lot Striping, Signage, Bollards, ADA Compliance and Upgrades, Catch Basins, Sweeping and Porter Services.
Whether you’re in need of a small repair or a new construction project, U.S. Pave's dedicated team has you covered.
For more information on our services contact us today at (954) 210-7481.